Modular Construction Methods: Volumetric vs. Panelized
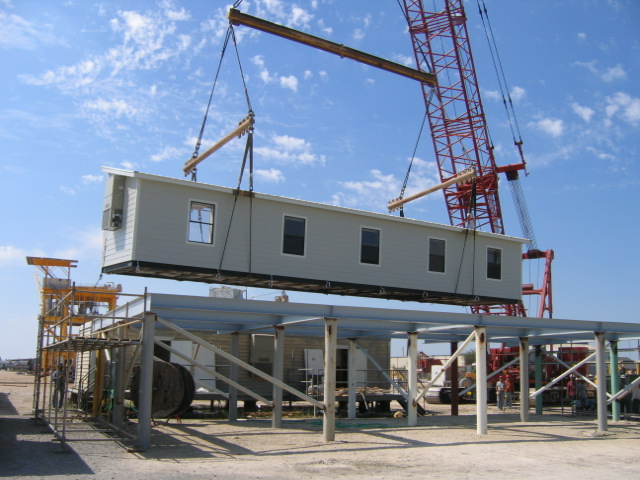
Modular construction has become a go-to solution for businesses across industries looking for efficient, cost-effective building solutions. But if you’re exploring modular construction for your next commercial project, you’ve likely come across two major methods: volumetric and panelized construction. Each has its own unique approach, benefits, and applications. In this blog, we’ll break down the differences between these methods and help you determine which might be the best fit for your project.
What is Volumetric Modular Construction?
Volumetric construction, sometimes called “modular buildings” or “modular boxes,” involves assembling entire sections—or modules—of a building offsite. These pre-built modules are constructed in a factory setting, complete with interior finishes, electrical systems, plumbing, and sometimes even furniture, before being transported to the construction site. Once delivered, they are stacked and connected like giant Lego blocks to form a complete building.
Pros of Volumetric Modular Construction:
- Speed: Since modules are built in a controlled environment and assembled simultaneously on-site, construction time is significantly reduced.
- Consistency: Factory settings allow for precise construction, reducing the risk of weather-related delays and quality control issues.
- Turnkey Solutions: Buildings can arrive nearly finished, minimizing the need for extensive on-site work.
Cons of Volumetric Modular Construction:
- Transportation Costs: Large modules require specialized transportation, which can drive up costs, especially for remote locations.
- Limited Design Flexibility: While volumetric modules offer many layout options, they can be less adaptable to unconventional designs or shapes.
What is Panelized Modular Construction?
Panelized construction, on the other hand, takes a different approach by building sections of walls, floors, and roofs in a factory setting. These panels are then transported to the site, where they are assembled much like a jigsaw puzzle. The panels are flat-packed, which makes transportation easier and more cost-efficient, but the assembly process on-site is more involved compared to volumetric construction.
Pros of Panelized Modular Construction:
- Design Flexibility: Since the structure is assembled piece by piece, panelized construction allows for greater customization and unique designs.
- Lower Transportation Costs: The flat-pack nature of panels makes them easier and more affordable to transport than bulky volumetric modules.
- Larger Buildings: Panelized construction is ideal for larger or more complex structures where volumetric modules might not be practical.
Cons of Panelized Modular Construction:
- Longer On-Site Assembly: While panelized systems are quicker than traditional construction, they require more on-site labor and assembly time compared to volumetric modules.
- More Coordination: Panelized construction requires precise coordination during assembly to ensure all pieces fit correctly, which can introduce complications if there are any site-specific issues.
Which Modular Method is Right for You?
Choosing between volumetric and panelized modular construction depends on your specific project needs. If you’re looking for a fast, turnkey solution for a relatively straightforward design, volumetric might be your best bet. However, if your project requires a more custom design or involves a larger structure, panelized construction could offer the flexibility and cost-effectiveness you need.
At Quick Buildings Modular, we specialize in delivering high-quality, custom modular solutions tailored to your unique project requirements. Whether you’re leaning toward volumetric or panelized construction, our expert team is here to help. Contact us today to discuss how we can bring your modular building vision to life.