Modular Vs. Traditional Construction: An Honest Comparison
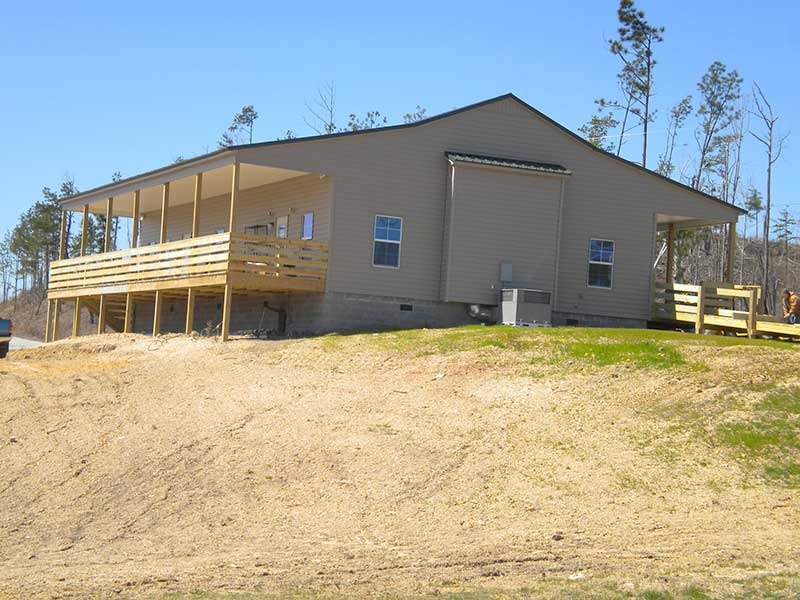
If you’re looking to expand or relocate your commercial space, you know the journey from blueprint to building is packed with crucial decisions. One of the first–and perhaps biggest–decisions you’ll face is deciding how your new space comes to life. Should you choose traditional construction or modular construction for your new commercial building?
Here at Quick Buildings Modular, we’re all about helping you make informed decisions that best suit your project needs. Although we specialize in modular buildings, we know traditional construction may be a better fit for some businesses. That’s why we’re diving deep into the details of modular vs. traditional construction. We’re here to lay out all the facts, compare apples to apples (or, more accurately, beams to modules), and guide you through the pros and cons of each method. Our goal? To arm you with all the info you need to make the best choice for your next big project.
To help you choose the right construction method for your new space, let’s discuss how the two compare in the following areas:
- Construction Process
- Applications
- Design and Customization
- Quality
- Speed
- Cost
- Sustainability
Construction Process
Modular Construction
Modular construction is a process that involves manufacturing building components off-site in a controlled factory setting, then transporting them to a project site for assembly and installation. These sections, or modules, are like 3D puzzle pieces. Once they’re made and delivered to your project site, the modules are connected and sealed together to form a functional building. It’s a bit like constructing a building with giant Lego blocks, and yes, it’s as cool as it sounds.
Traditional Construction
There are no secrets here: traditional construction is the classic way to build, where everything happens right on-site from the ground up. Workers bring materials to the site, foundations are laid, and the structure is built piece-by-piece and layer-by-layer. The majority of homes and buildings are brick-and-mortar structures made with traditional construction.
Applications
Modular Construction
Modules can be manufactured and assembled in a variety of sizes, styles, layouts and finishes. This versatility makes them ideal for a range of industries and applications. Some of the most common applications for modular buildings include:
Traditional Construction
Because traditional buildings are designed and constructed beam-by-beam, the potential applications are virtually limitless. Traditional construction can (and has) build commercial spaces for almost any use and industry, from general offices to industrial plants and science labs.
Design and Customization
Modular Construction
Modular buildings can be permanent or temporary (also called ‘relocatable’) spaces. Permanent modular buildings are designed to remain in place for long periods and are virtually indistinguishable from their traditional counterparts. Temporary modular buildings can be easily disassembled and repurposed for other uses or different settings.
Despite their factory-constructed process, modular buildings offer a wide range of design options and customizable features. They’re lighter and need fewer load-bearing walls, so modules can be easily connected to create interior layouts of various sizes and styles. The exterior and interior can be finished with a variety of materials, upgrades, and additions to meet industry requirements, streamline operations, or match your existing structures.
Traditional Construction
Unlike modular buildings, traditional construction is designed to create permanent structures that will remain largely unchanged for long periods of time. The design process is more intensive, as everything from interior walls and wiring to your building size, style, materials and finishes can be individually selected. While this provides more granular customization, many buyers feel overwhelmed by the amount of choices that must be decided before blueprints can be drawn and permits approved. Traditional construction can have a longer and more complex design process. Modular buildings can offer a wide variety of custom options in a shorter, streamlined design process.
Quality
Modular Construction
Modular buildings are built to the same building codes and with the same materials as traditional construction. Yet many modular buildings surpass their traditional counterparts in quality and consistency. That’s thanks to the highly controlled factory setting where modules are made to strict specifications. Materials are kept dry and away from the elements, and modules are inspected at various points to ensure quality control and design intent. The assembly process is also more precise and predictable, paving the way for long-lasting quality and durability. Modular construction has a highly-controlled setting and strict quality control measures to produce buildings that often surpass the standard building codes.
Traditional Construction
Traditional construction is often seen as the gold-standard in building quality, but the exposed and complex building process can create challenges in quality control. Weather events can damage materials left on the project site, and subcontracted workers may not meet the expected quality standards.
Speed
Modular Construction
Project speed is a key benefit of modular buildings. The nature of modular construction means steps can be completed simultaneously; while the modules are constructed off-site, the groundwork and foundation can be done and prepped for installation. The controlled factory setting where modules are made reduces the need for extra permits or inspections, as each module is built to strict codes and continually monitored. The factory-build process also reduces the impact of weather delays and vandalism. On average, modular construction projects can be finished 30 to 50% sooner than traditional builds according to the Modular Building Institute.
Traditional Construction
Traditional construction is a long and detailed process that follows a linear path: blueprints are drawn and submitted, permits are acquired, the site and foundation are built, then construction begins. There are required inspections and other factors that can delay or derail construction, including weather events, material damage, supply-chain issues and site disturbances. It can take weeks or even months to see notable progress in a traditional construction setting.
Cost
Modular Construction
Modular construction is an affordable alternative to traditional builds. Because modules are mass-produced in a factory, material and labor costs are significantly reduced. Faster completion times mean a quicker return on investment, allowing you to use your space sooner. Modular construction also creates less site disturbance, so you can keep operating while expanding your space.
Traditional Construction
Traditional construction projects come at a higher cost. Materials are more expensive, especially if they are sourced and delivered through different suppliers. Large construction teams and building specialists drive labor costs upward. Weather or shipping delays, material damage and other factors can unexpectedly lead to higher costs than originally predicted.
Sustainability
Modular Construction
Modular construction is smart and sustainable. The controlled factory setting reduces material waste and prevents trapped moisture, improving indoor air quality and energy consumption. Modular construction also causes less damage to the site and surrounding ecosystems. On top of a lower carbon footprint, modular buildings are easy to disassemble, repurpose and relocate, reducing the cost of raw materials and the energy needed for new builds.
Traditional Construction
Modern construction offers some green building practices, but usually at a higher cost. Traditional construction typically causes site disruption, noise and air pollution, and increased carbon emissions. Material waste, erosion, and runoff issues are common problems in traditional building projects.
Should You Choose Modular or Traditional Construction?
Deciding between modular and traditional construction is like choosing between a road trip and a flight. Each has its perks, quirks, and ideal scenarios. So, how do you decide which ticket to book for your next building project? It really boils down to what you value most: speed and efficiency, or customization and tradition? Let’s break it down to help you make that choice a little easier.
Go Modular If You:
- Have a tight timeline and need to start using your new building space as soon as possible.
- Have a leaner budget but still need a high-quality building that fits your needs and vision.
- Want a smart and sustainable space that’s good for your people and the planet.
- Need an adaptable space that can be reused, relocated or repurposed to meet future business needs.
Choose Traditional If You:
- Have a higher budget that can bend with unexpected costs or changing market conditions.
- Need to build on a challenging project site that needs specialized engineering or architectural oversight.
Quick Buildings Modular specializes in providing custom modular buildings to clients across the Southeast USA. Our modular buildings are fully customizable, built to the strictest codes and standards, and designed to expand your space quickly and affordably. If you think a modular building could be the best fit for your next project, contact our team to discuss your needs and request a quote. Let’s build something great together.
Read Next: